
Furniture for your garden
The metal garden bench is sure to make your neighbour green with envy. Also wouldn’t it be nice to see the look on their faces when you tell them you made it all on your own?
Richard Ostrowick and Peter Massingue show you how.
Materials
30mm x 5mm flat bar cut in the following lengths.
2 x 1.08m
2 x 880mm
2 x 440mm
10 x 1.2m
1 x 890mm
1 x 1.4m
2 x 1.15m
8 x 290mm
2 x 100mm rings
2 x spacers
4 x blank washers
Tools
Hammer
Tape measure
Clamps
Welding machine
Welding electrodes
Angle grinder
Vice
Vice-grip pliers
Pencil
Square
Project guide
Difficulty: Intermediate
Estimated time: 1 Week
Cost: R800
Step 1: Take the 1.08m pieces and bend one end of each into a V-shape for the feet. The other end of each piece you need to bend into a curl. For this, a jig was used, but you can use alternative methods to get the same effect.
Once this is done make a slight curve length wise in both the pieces. To see whether the two legs match, put them on top of each other and if they don’t line up go back to the vice and make some tweaks. Measured from curl to V it should be 910mm.
Step 2: For the front legs take the 880mm pieces and again bend one end of each into a V to serve as the feet. Take a tape measure and from the other end measure 350mm and make a mark. Put this mark against a round object and bend each piece into an L form. This time make a slight curve length wise between the foot and the L bend.
Step 3: To weld the front and back legs together measure 400mm from the V end of the back legs. Here you weld the front legs to the back legs. From the seat measure 325mm down on each leg and mark it. Weld the 440mm pieces on these marks to serve as support between the front and back legs.
Step 4: Put the legs on your work bench with the feet in the air. Now take 8 of the 1.2m pieces of flat bar. Now it’s the seats turn, starting from the back legs measure 30mm to get the mark where the last strip of flat bar should go. Leave a 25mm gap between each strip of flat bar and weld each strip to the legs working your way to the front. The 8th strip should be on the curve of the front legs.
Step 5: With the bench still up-side down, take the 890mm piece of flat bar. Make a curve in the one end according to the curve of the seat at the front. This is to give the seat some support. From the other end measure 475mm to indicate where to bend the flat bar so it can give support to the back of the bench. Once this is done find the centre of the bench and weld this piece to all the strips that serve as the seat.
Step 6: Now take the 1.4m piece of flat bar and make it into a big curve to serve as support between the legs from underneath. Weld it to the seat as well as the support pieces between the front and back legs.
Step 7: With the bench on its feet, measure 420mm upwards from the last seat strip. This is where one of the two remaining 1.2m strips of flat bar needs to be welded to. Also weld it to the back support in the center and cut of the excess piece. The last remaining strip is welded lower down to the back of the back legs in line with the front legs.
Step 8: The eight 290mm pieces and the 100mm rings are welded into the two rectangles of the back. Cut one end of each of the eight pieces at a 50 degree angle. The other ends need to be rounded inwards so it fits snuggly against the rings.
The angled ends need to go into the corners and extend to the middle where the rings are. You can choose to make the rings bigger than 100mm which would mean the pieces extending from the corners would be shorter.
Step 9: The remaining 1.15m pieces of flat bar needs to be bent into arm rests. Again here a jig was used to make the curls. The one end needs to bend into a curl and as it goes to the back make a slight curve in it. Again put both on top of each other to make sure they match.
The curled end is welded to the seat, but put a spacer between the arm rest and the seat. An off-cut piece of metal of 30mm will suffice. If you weld the arm rest directly onto the seat it creates a gap where water can easily gather and start to rust. The other end of the arm rest you weld to the back of the bench.
Step 10: Weld one blank washer onto each of the bench’s feet to give them some protection and to prevent the feet from sinking into the ground when it is soft.
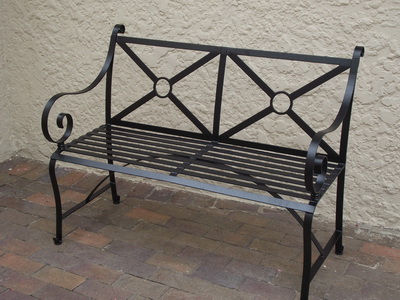
The finished garden bench

Make bends and curls in the back legs as well as curve them.

The L shaped front legs also get a V-bend at one end.

Weld the front and back legs together with the support in between the two.

From the back legs measure 30mm to know where to weld the last seat piece.
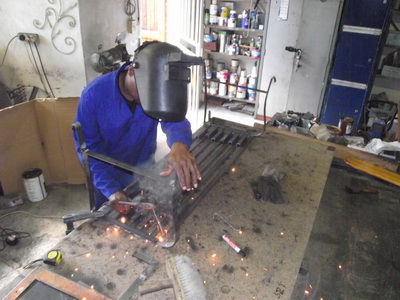
Working your way to the front weld each seat piece on.

The last seat piece needs to go on the curve of the front legs.

Weld this on the seat to provide support as well as form part of the back.
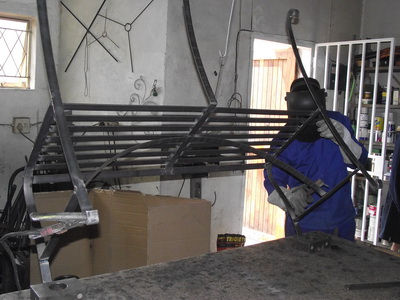
The curved flat bar underneath to provide stability to the whole bench.

Weld the top back piece to the legs and the centre piece.

The bottom back piece.
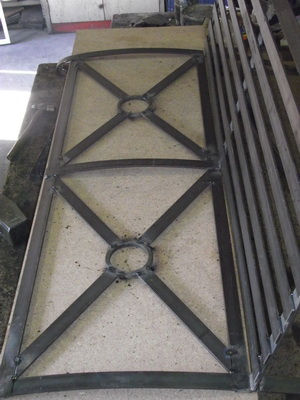
The rings suspended in the rectangles of the back.

The arm rests welded to the seat and back.

Weld the washer to the feet to provide extra protection.
